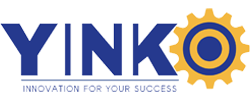
High-speed Cup Screen Printing Machine with PLC control, servo alignment, and automatic feeding. Ideal for multi-color printing on PET, PP, glass cups, and bottles—even without registration marks.
Model No :
YK-400YProduct Name :
Cup Screen Printing MachinePower Supply :
220V 50HZ /60HZProduction Capacity :
900PCS/HOURUsage :
Logo PrintingShipping Port :
Shanghai,Ningbo,Shenzhen,Lead Time :
10daysWeight :
280kgThis cup screen printing machine adopts PLC control with digital HMI (human-machine interface) operation. The equipment utilizes a servo + cursor positioning system for precise alignment.
It offers multiple function settings and can achieve multicolor registration printing even for products without registration marks. Featuring innovative structural design combined with a three-axis servo motor curvature operation system, this model is specifically customized for multi-color printing of unregistered products.
• High-Speed Printing: Designed for rapid and efficient multi-color printing.
• Automatic Feeding System: Improves production line automation and reduces labor.
• Precision Screen Printing: Suitable for cylindrical, round, and irregular-shaped containers (like cups and bottles).
• Applications: PET bottles, PP cups, glass bottles, cosmetic containers, tubes, mugs, etc.
• Adjustable Settings: Easily change printing size and parameters for different products.
• Durable Build: Heavy-duty metal frame ensures stability and longevity.
1. Intelligent Microcomputer IC Control
Equipped with touch-sensitive panel for program compilation
Simplified operation with precise, reliable motion control
2. Built-in 4-Digit Automatic Counter
Ensures accurate production tracking
3. Adjustable Printing Stroke & Speed
Customizable settings for diverse printing requirements
4. Fully Automated Printing Cycle
Auto blade scraping, ink return, and platform lifting
Ensures consistent print quality with minimal operator intervention
5. Auto-Balanced Squeegee System
Maintains uniform printing pressure for optimal results
6. Precision Micro-Adjustable Worktable
Allows fine left/right and up/down screen frame adjustments
Delivers high print accuracy with quick setup
7. Premium German FESTO Pneumatic Components
Guarantees superior machine performance and reliability
NO |
Item |
Specification |
1 |
Max. Printing Area |
300mm × 450mm |
2 |
Max. Screen Frame Size |
500mm × 680mm |
3 |
Product Diameter |
Ø10mm– Ø180mm |
4 |
Registration Accuracy |
±0.05mm |
5 |
Control System |
Hitachi PLC |
6 |
Touch Panel |
Weintek HMI |
7 |
Positioning System |
Servo + Cursor Positioning |
8 |
Cycle Time |
Approx. 4 sec |
9 |
Working Air Pressure |
0.4–0.6 MPa |
10 |
Machine Structure |
Modular Design |
11 |
Production Capacity |
Approx. 900 pcs/hour |
12 |
Power Supply |
220V, 50/60Hz |
13 |
Machine Dimensions (L×W×H) |
1050mm × 1250mm × 1750mm |
14 |
Machine Weight |
Approx. 280 kg |
Section |
Item |
Component |
Configuration Details |
Print Head Left/Right System |
Drive Mechanism |
Servo Motor |
Fuji Electric (Japan) |
Guide Mechanism |
Ball Screw |
HIWIN |
|
Print Head Up/Down System |
Drive Mechanism |
Servo Motor |
CHENBONG (Shinbao) |
Guide Mechanism |
Linkage Bearing |
OMRON |
|
Control System |
Control Circuit |
PLC + HMI |
Hitachi (Japan) |
Pneumatic Control |
Solenoid Valve |
SMC |
|
Servo Rotation System |
Drive Mechanism |
Servo Motor |
Fuji Electric (Japan) |
Guide Mechanism |
Rotary Bearing |
OMRON |
|
Cursor Alignment System |
Lens |
Industrial Lens |
Dahua Technology |
System |
MKC400 |
Maikecheng (MKC) |
The choice of machine is unrelated to the material; what is important is the product specifications and the printed pattern.
• Packaging industry—e.g.cosmetic bottles, cream jars, food containers
• Drinkware manufacturing—e.g.mugs, plastic cups
• Pharmaceutical & chemical bottles—e.g., pill bottles, chemical reagent bottles
1. Shutdown Protocol
Power off the machine and disconnect the air supply at the end of each shift.
Wipe down all external surfaces to maintain cleanliness and prevent debris buildup.
2. Pneumatic System Maintenance
Regularly drain accumulated moisture from air filters to prevent corrosion.
Refill the lubricator (oil mist unit) with ISO VG32-grade pneumatic oil as needed.
3. Short-Term Storage (Hours)
Remove the squeegee assembly from its holder and place it in the ink reservoir.
Position the carriage at the forwardmost position.
Before resuming operation: Dilute residual ink with solvent, reinstall the squeegee, then commence printing.
4. Extended Shutdown (Days)
Completely purge all ink from the reservoir using approved cleaning agents.
Apply corrosion inhibitor to bare metal components if storing beyond 72 hours.
5. Mechanical Lubrication
Apply high-temperature lithium complex grease (NLGI #2) to all pivot points and sliding mechanisms.
Focus on:
• Guide rail bearings
• Linkage joints
• Elevation screw threads
6. Contamination Control
Implement Class 1000 cleanroom protocols for critical printing areas.
Install positive-pressure dust curtains around the machine perimeter.
Use antistatic wipes for optical components and precision guides.